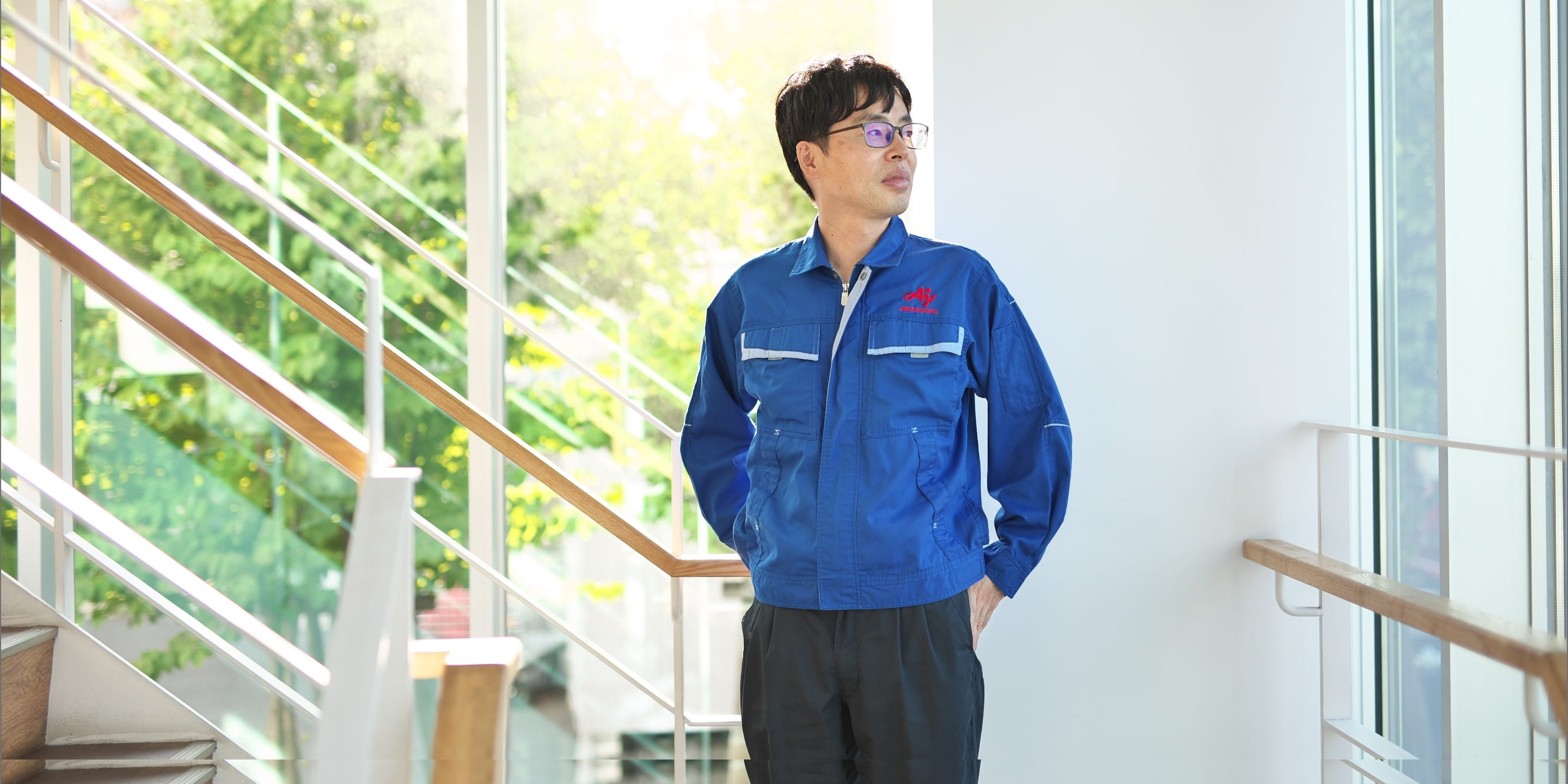
project story_02
近未来の工場DXを視野に
ABF工場の自動化・ICT化を推進
昨今、製造業が激しい環境変化に対応しながら成長するために、工場の自動化・ICT化の重要性が増しています。しかし、味の素ビルドアップフィルム®(ABF)の塗液(以降、ワニス)を生産するラインでは、日々高度化するユーザーニーズに応えるべくフレキシブルな対応が必要なため、単純な自動化・ICT化は困難とされてきました。フレキシビリティを維持しつつ自動化・ICT化するにはどうすればいいのか。ワニスの量産工場の自動化・ICT化プロジェクトは、この大きな課題を抱えて始動しました。
member
-
群馬工場長 基礎工学研究科
化学工学専攻
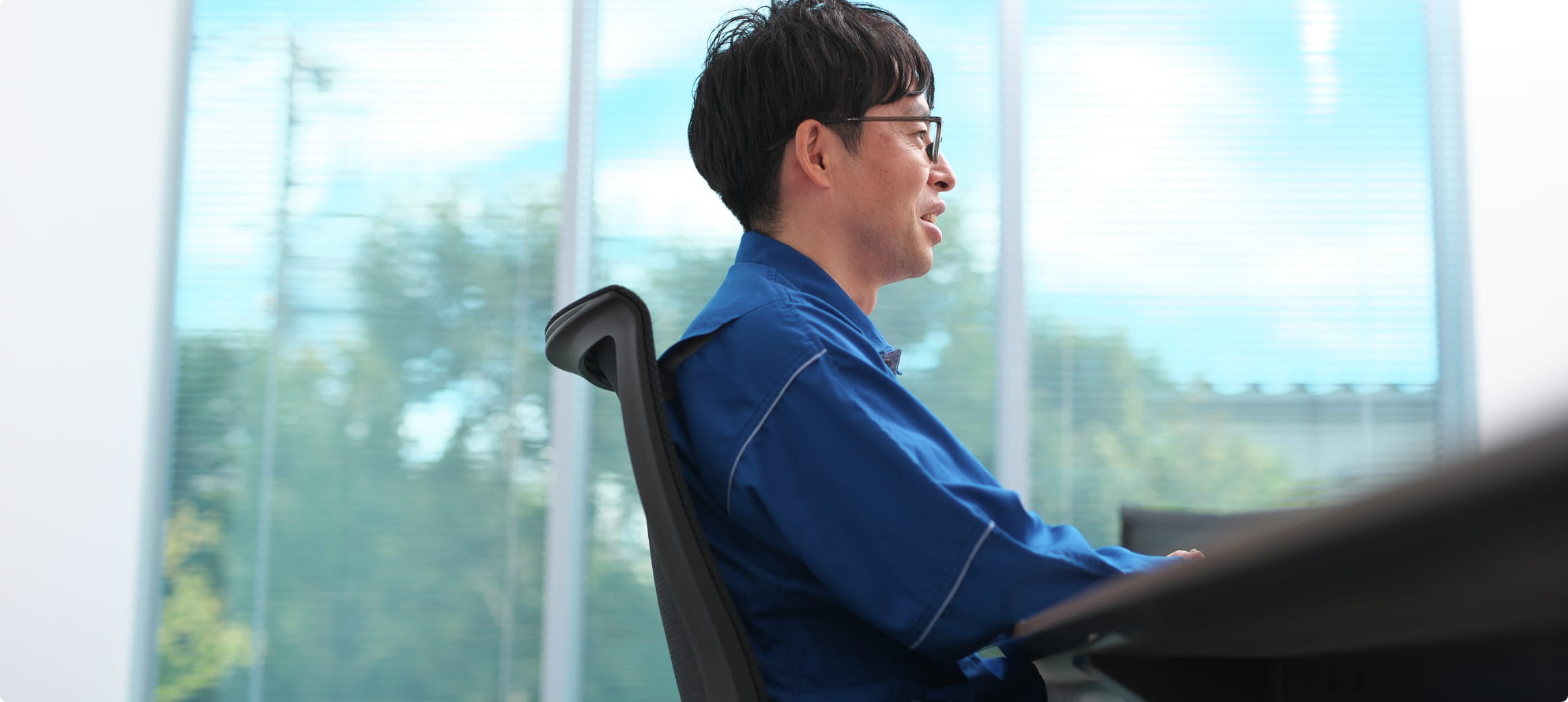
STORY_01
製造部門の多大な
作業負荷という積年の課題
その改善だけではなく、
先を見据えたゴールの設定
これからお話するプロジェクトは、圧倒的な世界シェアを誇るABFの素となる、ワニスの生産ラインの自動化・ICT化を実現することを目的に推進されました。主たる目標は製造部門の負荷軽減と生産性の向上です。量産工場では重量物を取扱う作業で肉体的な負担が大きく、さらにはミス防止に細心の注意を払う必要があるため心理的な負担も大きい、という積年の課題がありました。そして生産量増加によりますます負担が増しており、これら課題の解決は待ったなしの状況となっていました。これらを解決するため、重量物取扱い作業に自動化設備を導入して肉体的負担を低減すること。そしてICTを活用したミス防止技術を導入して精神的負担を低減すること。これらにより、製造部門メンバーの心身両面の負担を軽減しながら生産性も向上させ、生産量増加に対応することがプロジェクトの目指すゴールでした。
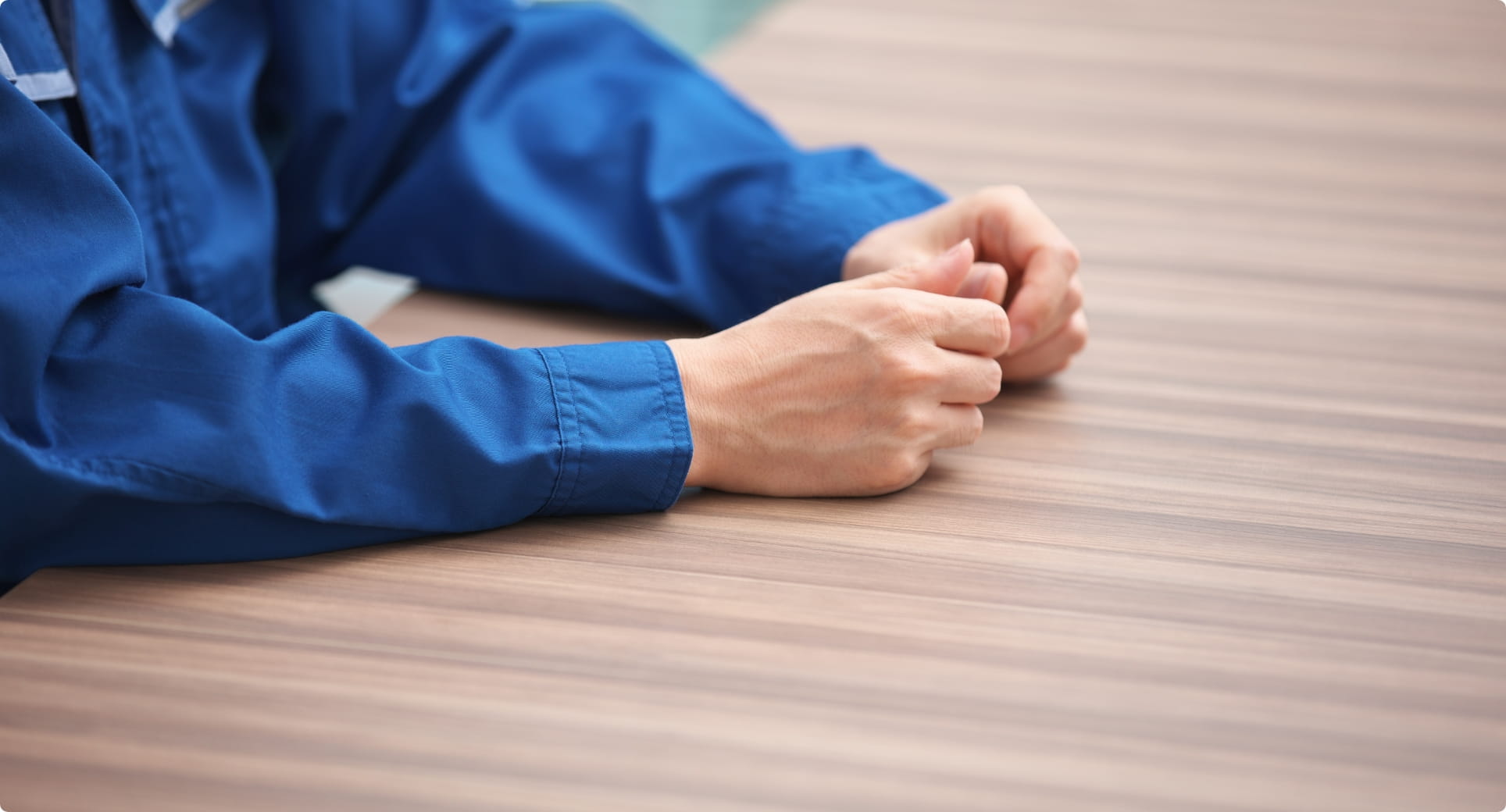
STORY_02
描いたグランドデザインを
実現するため
これまでの経験を最大限に
活かして可能性を探る
ABFが使用される半導体業界は技術革新が目まぐるしく、ユーザーニーズは日々変化しています。そのため、原料のワニスの生産現場では、いわゆる大量生産型の生産現場とは異なり、市場ニーズを先取りするように製法を変化させるフレキシビリティが求められます。その点が自動化を阻む大きな要因になっていました。
プロジェクト立上げ前から「量産工場の自動化推進」をミッションとして全社の工場自動化におけるボトルネックについて検討を続けており、先述の課題についても把握していました。そこで多くの製品に共通する工程の中から特に重量物取扱いが多く、かつ製法変化の影響が小さい工程をピックアップし、その工程に自動化設備を導入する。併せて製造指示書と記録書等の帳票類の情報を電子帳票化してデジタルシステムを構築することによりヒューマンエラーの軽減にも取り組む。という全体図を描きました。プロジェクトでは自動化設備と電子帳票システムの開発、それぞれに担当者を配置し、担当者が全体最適を考えながら関係者と協力して技術を具現化できるようにプロジェクトをマネジメントしました。併せて、電子帳票システム開発ではシステムの構想を考えるとともに、製造部門メンバーと協力しながら開発実務も担当しました。

STORY_03
生産現場ならではの
無数の“暗黙知”
味の素ファインテクノの社風が解決のカギに
電子帳票システムの開発においては、現状の作業方法とミス防止方法が複雑で、製品ごとに方法も異なるため、一般的な工場のシステム化手法を当てはめることは困難でした。そのため、製造部門と意見交換を重ね、システム開発会社の協力も得ながら、フレキシビリティが求められる当社の生産ラインに最も適した電子帳票システムの在り方とは何か、どうすれば現場負担を軽減し、ミスを軽減するシステムを実現できるか、試行錯誤を繰り返す日々が続きました。これまでシステム開発の経験はありませんでしたが、IT戦略の資格取得などを通してスキルを高め、当社ならではのシステム構想を立てるに至りました。
文化されていない生産現場のノウハウを、自動化設備やシステムでどのように実現するかという点にも苦労しました。一般的に生産現場では、経験に裏付けられた無数の“暗黙知”が存在しています。それらを無視して自動化・システム化を進めても、決して良い結果は生まれません。このプロジェクトでも、実証実験を進めてみると、「この作業はこの点が重要で、このような工夫を行っている」、「稀にしか発生しないが、このようなケースにも対応する必要がある」など、製造指示書や現場観察からは読み取れなかった多くの意見が現場から出てきました。当社は部門間の距離が近く、コミュニケーションも良好なため、実証実験においても製造部門が積極的に協力してくれました。製造部門を巻き込み、システム開発会社や設備メーカーと議論を重ねることで、生産現場の“暗黙知”を言語化することに成功。それらを機能に反映することで、現場で使いやすく安定的に稼働する設備やシステムにすることができました。
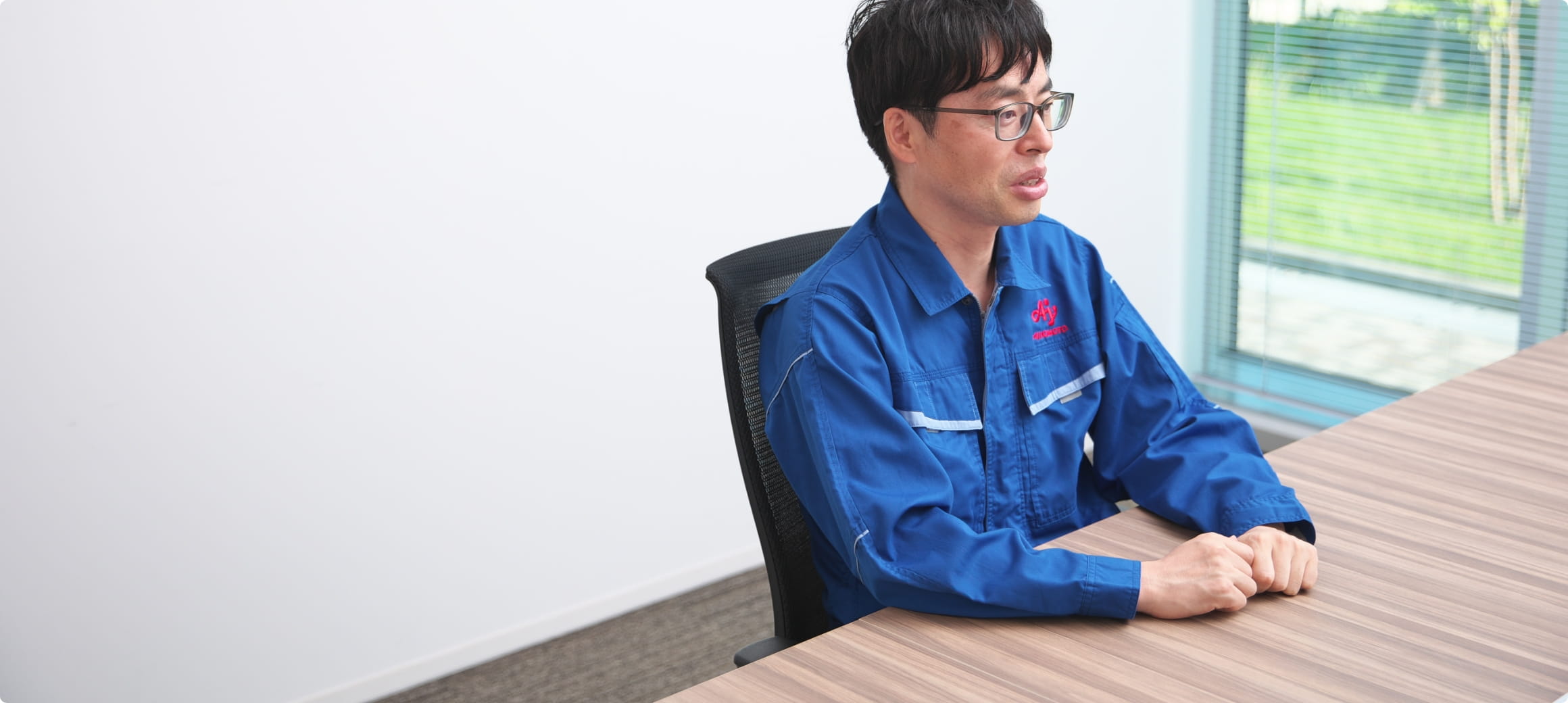
STORY_04
社内から得られた
高い評価を糧に
全社的な展開と
未来予想図を描く
このプロジェクトでは、安定生産への貢献を特に意識しました。電子帳票システム開発では、単に帳票類をデジタル化するにとどまらず、AIを活用して人間の目視確認をフォローする機能を実装するなど、ミスを減らす技術を多く取り入れました。自動化設備開発では、作業者に危険が及ばないよう安全対策を十分に施すとともに、連続運転やメンテナンス作業も考慮し、安定的に稼働し続ける設備であることにこだわり、プロジェクトを通じてこれらの目標を達成してきました。現在は量産工場の生産ラインのひとつで自動化設備と電子帳票システムが稼働しており、工場のメンバーからは「作業効率が上がった」、「ミスのリスクが減った」という前向きな評価を得ています。自分たちで考え導入した技術が役に立っているという実感、このプロジェクトで得た経験や知見は、会社の大きな財産になりました。
その一方で、これらの技術は量産工場の一部の生産ラインに導入したのみです。この技術を改良しながら、今後は量産工場の全てに導入を進めるとともに、さらなる新技術を開発・導入することで、安定した品質で生産性の高いモノ作りを実現し、かつ作業負荷や環境負荷の小さい工場の実現を目指します。とりわけデジタル技術の発達は著しいものがあり、今後は工場のDXをどのように推進していくかが全社的な課題になります。デジタル技術でモノ作りをトランスフォームしていく。そのためには、このプロジェクトで体現した「暗黙知を言語化していく」というプロセスが不可欠です。そうした近未来の工場DXを視野に入れつつ、今後も当社は研鑽を重ねていきます。
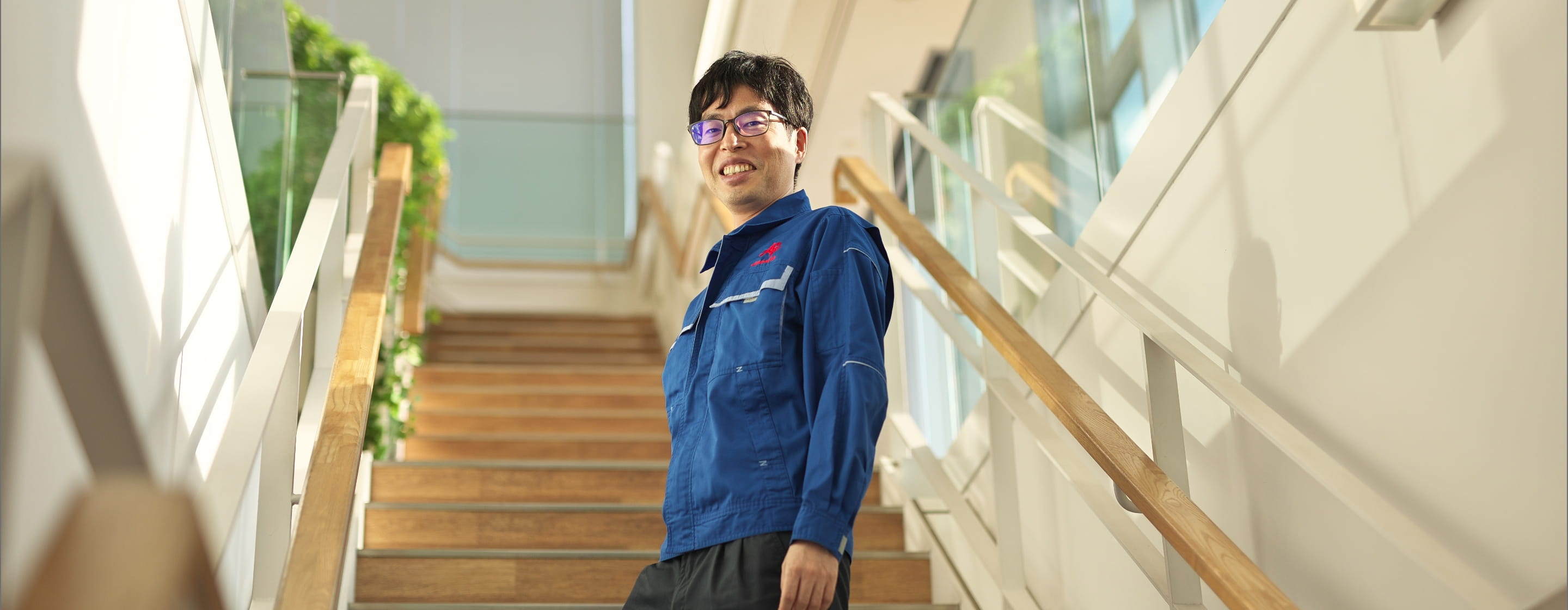
※部署名は撮影当時のものです